The Daiichi Sankyo Group of companies stipulates in Article 2 of
the Daiichi Sankyo Group Corporate Conduct Charter
that “we respect international norms, diverse cultures and customs, conduct business in a fair manner through free and fair competition, and conduct responsible procurement by complying with laws and regulations in each country and region in which we do business.” In addition, we have incorporated measures for sustainable procurement in
the Daiichi Sankyo Group Procurement Policy.
We will continue to make high effort to put into practice our corporate mission of “contributing to the enrichment of quality of life around the world through the creation of innovative pharmaceuticals, and through the provision of pharmaceuticals addressing diverse medical needs,” while aiming to contribute to a better society, environment, and economic development through promoting sustainable procurement activities.
Business Partner Code of Conduct
The Group has established its Business Partner Code of Conduct based on the Daiichi Sankyo Group Procurement Policy. This code sets out our expectations for our business partners who provide products and services to us to help creating a sustainable society. We are committed to fulfilling our social responsibilities and achieving a sustainable society through communicating and working together with our business partners.
Daiichi Sankyo Group Procurement Policy
Business Partner Code of Conduct
Promotion of Sustainable Procurement Activities
We conduct a “Sustainable Procurement Survey” with key business partners on a three-year cycle in order to confirm their understanding of and alignment with the Group's approach to sustainability and to strengthen interactive communications.
In this survey, respondents are asked to answer some questions related to the following six areas based on the Business Partner Code of Conduct: “business activities with integrity based on ethical standards,” “respect for human rights and labor,” “health and safety,” “promoting environmental management,” “securing optimal quality, cost, and stable supply,” and “management systems”. The survey is also aligned with the principles of the PSCI*1, a non-profit organization composed of global pharmaceutical companies.
During the cycle covering the period of 2020-22, the survey was sent to 403 business partners of Daiichi Sankyo in Japan and overseas, and as of the end of March 2023, 399 companies (99%) have responded. Based on the survey results and scoring, further communications with 20 selected business partners were conducted. Also, 30 of those key business partners took our training on Environment. We have started our 3rd survey cycle using a updated questionnaire. Through those surveys and internet communications, we continuously promote our efforts in sustainable procurement and foster a mutual understanding with our business partners on the importance of sustainability to our social responsibility.
The questions of 3rd cycle of Sustainable Survey
Sustainable Procurement Survey Progress
The Group companies mitigate potential risk related to business partner selection and ongoing relationships through due diligence assessments, which begin at the outset of business partner onboarding and continue through regular monitoring in the fields of corruption, data privacy and confidentiality, human rights and environmental protection. We are monitoring approximately 6,400 companies at this point. In Japan, Daiichi Sankyo established the Business Partner Management Guideline (Japanese version), which summarizes the Business Partner Management process, in September 2021. For Group companies overseas, the Daiichi Sankyo Group Business Partner Management Guidelines (Global Guidelines) were established in October 2022. Since then, the Daiichi Sankyo Group has conducted business partner risk assessments globally using an IT supported system, information about the business partner where publicly available, as well as business partners’ responses to indicative questionnaires. Risk assessments in each risk area are based on the combination of ① the attributes of business partners such as countries and industries based on CPI Score*2 and ILO Score *3, and ② the results of questionnaire responses collected from the business partners. If a business partner alert is detected prior to or during transactions, the Daiichi Sankyo Group has instituted mitigation measures such as conducting individual interviews and requesting suggestions for improvement measures according to the nature and degree of the identified risk for the business and the social credibility of the Daiichi Sankyo Group. In FY2023, Daiichi Sankyo Japan conducted such actions with 3 business partners. Additionally, we also conduct reevaluations of risks as necessary. Through these measures, Daiichi Sankyo aims to realize long-term, sustainable social contribution.
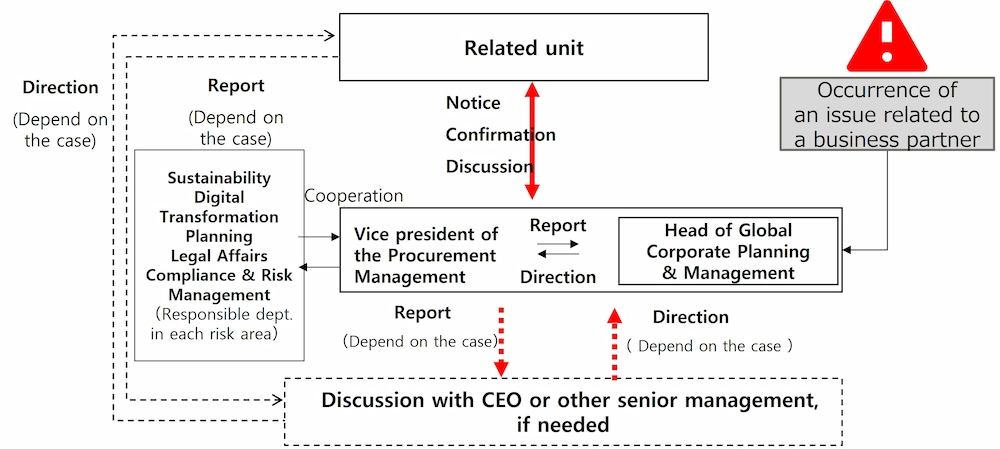
*1 PSCI (Pharmaceutical Supply Chain Initiative) is a non-profit membership organization formed by large pharmaceutical companies with the objective of improving social, economic, and environmental outcomes through the supply chain. It aims to ensure safe working conditions for workers, promote sustainable processes and factory facilities, contribute to economic development, and maintain a clean environment in local communities.
*2 CPI is a corruption index published by Transparency International. The index has been compiled since 1995 and is published in the form of a ranking that compares the perceived level of corruption in the public sector of 180 countries worldwide.
*3 ILO (International Labor Organization) is calculated by our company based on the country-specific indicators for four human rights issues related to core labor standards (forced labor, child labor, discrimination, and freedom of association and collective bargening).
Reinforcing Compliance in Procurement
In order to realize responsible procurement activities, the Daiichi Sankyo Group of companies introduced a procurement purchasing system in FY 2020 to promote fair and sound transactions and launched catalog transactions for certain goods in October 2020. By expanding the scope of transactions using this procurement purchasing system, we are working to increase the transparency of transactions and further reinforce compliance in procurement. Trainings are provided periodically to employees engaged in procurement activities. In Japan, we hold seminars on the Act against Delay in Payment of Subcontract Proceeds. every year. In May 2024, an online seminar was held for seven companies, including main group companies in Japan, and approximately 150 people in charge of the Subcontracting Act from each division participated. We will continue to provide similar trainings to raise awareness of compliance in procurement.
Measures to Ensure Stable Procurement
In recent years, many companies are facing unprecedented natural disasters, infectious diseases, and geopolitical risks. Maintaining and stabilizing the supply chain, not limited to Tier 1 suppliers, but including Tier 2 or 3, which are upstream suppliers, is challenge. In Japan, we conducted a retrospective assessment of suppliers covering approximately 1,200 raw materials for our five main plants in Hiratsuka, Odawara, Onahama, Tatebayashi and Kitamoto to understand geographical risks. Of these, we asked Non-Tier 1 suppliers of critical raw materials, upstream suppliers of raw materials for our products that have no direct contracts with Daiichi Sankyo, to complete the above Sustainable Procurement Survey. While seeking an understanding of our policy and strengthening co-creation relationships through mutual understanding, we will continue to reinforce our efforts for stable procurement through interactive communication with our business partners.
Geographical distribution and spend analysis of Tier 1 suppliers for five main plants*
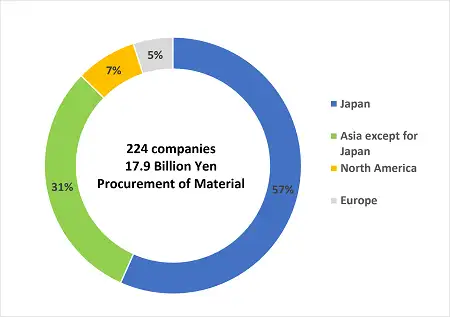
*Direct materials for five main plants (Hiratsuka, Odawara, Onahama, Tatebayashi and Kitamoto), based on FY2022 Procurement Amount
Implementation of Quality Audit for Raw Material Suppliers
In order to ensure the quality of our pharmaceutical products, Daiichi Sankyo Group systematically conducts audits on domestic and overseas suppliers of raw materials, active pharmaceutical ingredients (APIs) and drag products, etc. The Group confirms the status of manufacturing and quality control systems through on-site monitoring during manufacturing and/or testing, if necessary. Remote audits are one of the new solutions to cope with special situation such as the COVID-19 pandemic. The audit scope, method and frequency are determined based on the quality risk assessments. The Group has been striving to maintain and improve quality of our products under the spirit of “Quality first” to stably supply top-quality pharmaceutical products to patients.