Basic Policy
The Daiichi Sankyo Group recognizes environmental issues, including global warming and extreme weather, as critical challenges affecting our lives and work, and also as risk factors that may impact our long-term business activities. The Group believes that promoting environmental management will contribute to the development of a sustainable society and help establish a foundation for its long-term corporate growth.
Daiichi Sankyo Group EHS Policy
The Daiichi Sankyo Group has established a global policy to express its commitment to protecting the environment and ensuring the health and safety of our employees as fundamental corporate responsibilities.
The Daiichi Sankyo Group has implemented EHS initiatives based on the recognition that protecting the environment and ensuring the health and safety of our employees throughout every aspect of its corporate activities constitutes key management issues.
We comply with the related applicable laws and regulations of each country as well as international agreements for protecting the environment and ensuring the health and safety while setting even higher goals that we strive to exceed.
We maintain a management system, in which organizational roles and responsibilities are clearly defined for continuous improvement as a means of thoroughly protecting the environment and ensuring the health and safety of our employees.
We strive to increase the knowledge of our employees through training and educational activities in order to raise their awareness of the need and means for environmental issues and concerns.
We actively communicate information to stakeholders on the Daiichi Sankyo Group‘s efforts to protect the environment and ensure the health and safety of our employees.
EHS Basic Policy
- Reduce environmental impact in the Group's business processes and supply chain, from research and development to production, distribution, use, consumption, and disposal
- Improve the working environment so that employees can work safely and maintain and promote their health
- Establish, operate, evaluate, and improve the EHS management system
- Comply with environmental and health and safety related laws and regulations
- Reduce EHS risks and eliminate sources of hazards
- Efficient use of resources and energy, reduction of greenhouse gas emissions, appropriate use of water and wastewater management, waste reduction and recycling, respect for biodiversity, appropriate management of chemical substances, and prevention of deforestation
- Prevent health hazards and occupational accidents
- Engage in EHS education and awareness-raising activities
- Participate in EHS communication and consultation with internal and external stakeholders
Promoting Environmental Management
We conduct business activities to contribute to the enrichment of quality of life through providing pharmaceutical products. We know, however, that those activities could cause environmental impact that might raise environmental issues. What underlies our promotion of environmental management is the following belief: activities necessary to provide pharmaceutical products must not unnecessarily contribute to environmental phenomenon that may threaten people’s health and daily lives. Therefore, for our 5-Year Business Plan (FY2021-FY2025) we are taking on a wide range of challenges to reduce our environmental load in everything from research & development (R&D) to sales across the entire value chain, to contribute to realizing a sustainable society. Taking these sustainability challenges into consideration, we established EHS Management Policy (FY2021-FY2025) to promote environmental management.
Reduction of Environmental Impact Across the Entire Value Chain
Implement various initiatives to reduce environmental impact
and contribute to society and the environment
- Social and
environmental
challenges
- Decarbonized society
- Circular economy
- Society in harmony
with nature
- Daiichi Sankyo’s
Long-term targets
(for 2050)
- Carbon neutral
- 100% recycling
- Minimize environmental risk
Initiatives throughout the value chain
Research and Development
Pharmaceutical Technology
Supply Chain
Offices, Sales
- DX utilization
- Chemical substances mgt.
- Green Chemistry*1
- Bioplastics utilization
- Renewable energy
- Collaboration with suppliers
- Next-generation batteries
- Hydrogen utilization
- *1 Manufacturing process in consideration of the sustainability of the global environment, including prevention of environmental pollution, and reduction of raw material and energy consumption
- *2 Net Zero Energy Building
EHS Management Policy (FY2021-FY2025) and Environmental Management Targets (Numerical Targets and Main Activities)
The 5-Year Business Plan defines the following three main targets as our long-term vision for 2050 to realize a sustainable society: “carbon neutrality” to achieve a decarbonized society, “100% recycling rate” to strive for a circular economy, and “minimization of environmental risks” to fulfill our responsibility to realize a society that is in harmony with nature.
With the growing social demand for carbon neutrality, we revised the target to a more ambitious one in June 2022. Specifically, we have changed our CO₂ emission reduction targets to 42% in FY2025 and 63% in FY2030 compared to FY2015, which are consistent with a “1.5°C target” of the Paris Agreement. This target has been approved as 1.5℃ targets by the SBTi in June 2023. To achieve these targets, we switched the electricity used at our head office building and all of our plants and research centers in Japan to electricity from renewable energy sources in FY2022. As a result, we achieved a 49.6% reduction in global CO2 emissions (Scope 1 + Scope 2) against our FY2025 target of a 42% reduction from FY2015. In addition, our renewable electricity utilization rate was 78.1% against our target of at least 60% in FY2025. For FY2030, we aim to achieve a renewable electricity utilization rate of 100% as set forth in RE100*4 as soon as possible. Furthermore, to enhance the sustainability of the entire supply chain, we established a target of having at least 70% of our business partners set a 1.5°C level target by 2025, and in FY2022 we joined the CDP Supply Chain Program of CDP, an international environmental non-profit organization. Through this program, we will promote initiatives to reduce CO₂ emissions with our business partners. In order to reach our FY2030 targets and achieve carbon neutrality by 2050, we will continue to further promote the use of renewable energy for electricity and improving the efficiency of energy-consuming equipment such as boilers and air conditioners.
FY2025 and FY2030 Target toward Carbon Neutrality
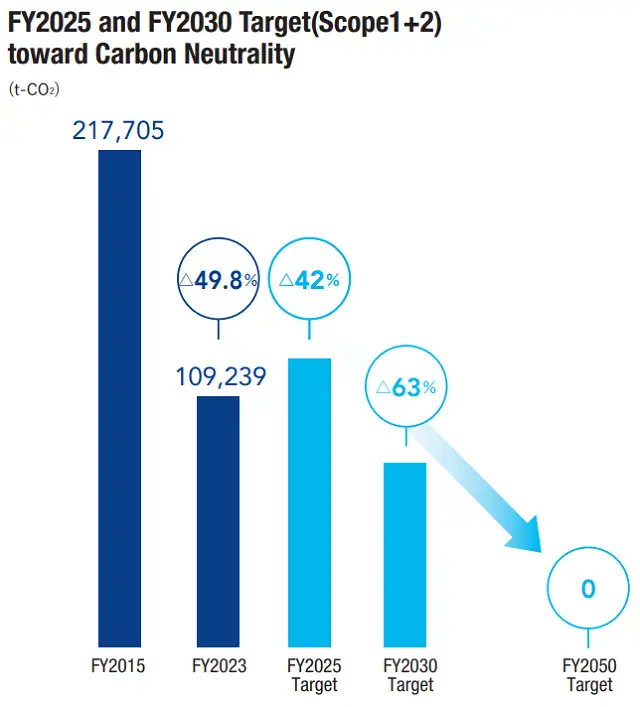
Furthermore, we have expressed our support for the GX League*5, which was established by the Ministry of Economy, Trade and Industry towards achieving carbon neutrality by 2050, and we will participate in the carbon-credit-market demonstration project to be started in September of 2022.
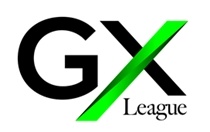
- *3Acronym for Task Force on Climate-related Financial Disclosures. It is a task force that was established in December 2015 by the FSB, an international organization participated in by central banks and financial regulators of major countries.
- *4 Acronym for Science Based Targets initiative. International initiative that encourages companies to set greenhouse gas emission reduction targets consistent with the levels required under the Paris Agreement.
- *5 To achieve carbon neutrality by 2050, it was established as a forum for companies that actively engage in GX (Green Transformation) that brings together industry, government, academia, and financial sector, to hold discussions on reforming the entire economic and social system for GX, and to pursue the creation of new markets.
5-Year Business Plan(FY2021-FY2025)
Materiality and KPI
Basic Biodiversity Principles and Action Guidelines
Sustainable Procurement
EHS Management Promotion System
Since the establishment of an Environmental Management Committee in 2007, we have continued to implement environmental conservation activities from a mid-to-long-term perspective. We have conducted these activities by setting out targets for global warming countermeasures, reduction of waste, and others in the Fourth Medium-term Environmental Management Policy and monitoring the progress in accordance with the policy. In April 2019, in order to address the environment, health, and safety issues, as required by the international community, in an integrated manner, we established the Daiichi Sankyo Group EHS Policy and the EHS Management Committee as a corporate governance system organization for the purpose of strengthening the EHS management system. In 2024, we launched the Sustainability Committee, composed of global members, to oversee this management system.
The Head of Global Corporate Strategy serves as the Head of Global EHS Management, overseeing EHS management across the group, while the Head of Global Sustainability serves as the Global Environmental Management Officer and the Head of Global HR serves as the Global Health and Safety Management Officer, promoting EHS management. We have built appropriate EHS management systems that takes regional and unit structure considerations into account and establish EHS management sites as necessary while overseeing targets. The Sustainability Committee, chaired by the Head of Global Corporate Strategy, deliberates on policies, EHS Management Action Plan, and implementation reports regarding EHS management. The results of these discussions are escalated to the Executive Management Committee (EMC).
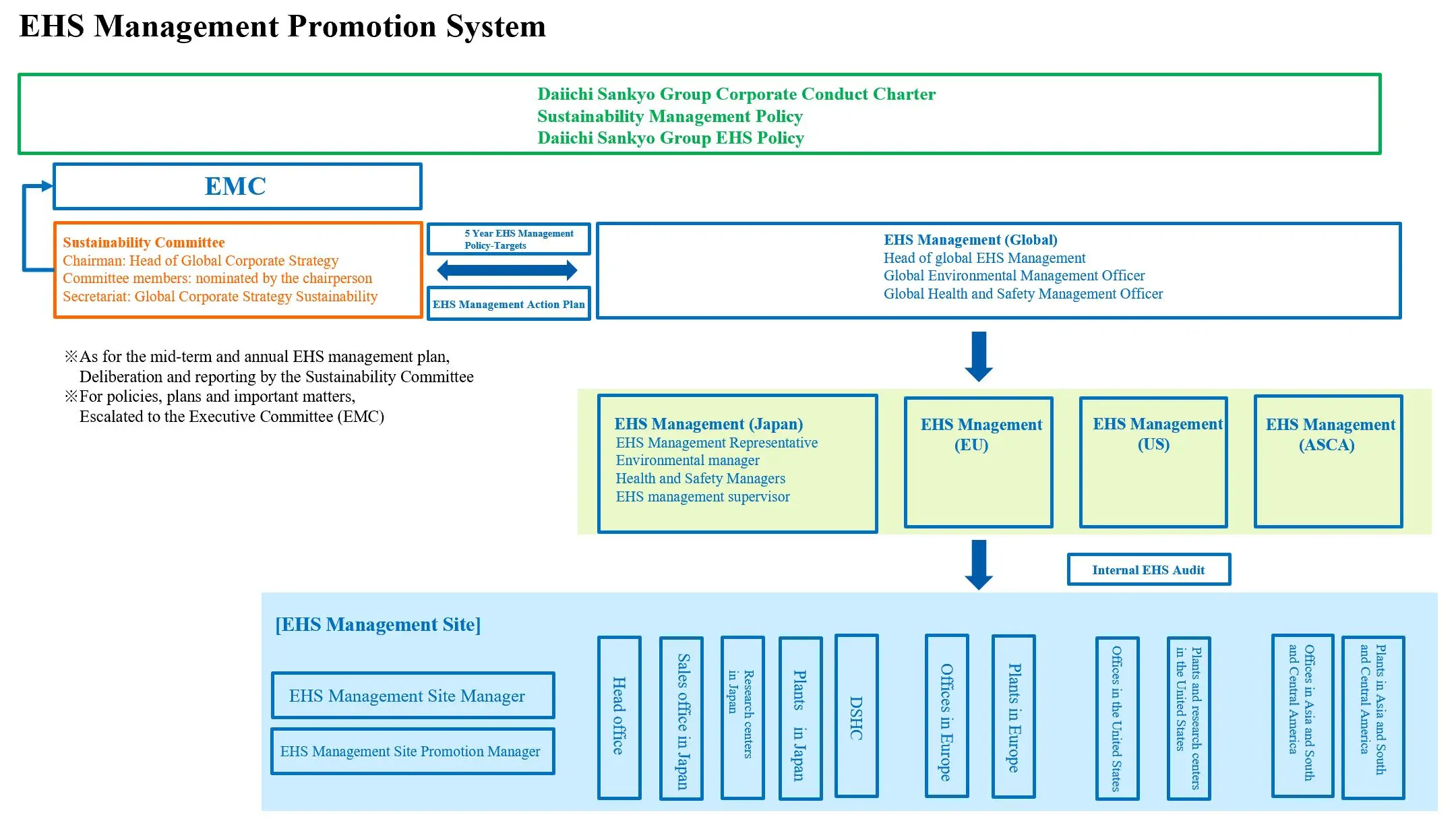
Environmental Auditing
ISO 14001 Certification
Optimization of the environmental management system (EMS)
The Daiichi Sankyo Group promotes the optimization of the EMS in accordance with the Standard for the Daiichi Sankyo Group’s Environmental Management Systems.
Operating (production) sites that use large amounts of energy for manufacturing in Daiichi Sankyo Group have acquired the international standard for the EMS, ISO14001 certification (See the table below). We have also acquired ISO14001 certification in a multi-site registration that integrates all production sites of Group companies in Japan in one certification scope.
Furthermore, of our overseas Group companies, the Shanghai Plant in China, the Altkirch Plant in France, the Pfaffenhofen Plant in Germany, and the Alphaville Plant in Brazil have acquired ISO14001 certification, bringing the acquisition rate of the certification at production sites to 89.3% (on the basis of FY2023 energy consumption). The plants that have not acquired ISO14001 certification are also working to receive certification.
The Daiichi Sankyo Group continues to strive to optimize the environmental systems within the entire Group to reduce environmental impacts and risks throughout all business activities.
List of operating sites that have acquired ISO14001 certification (as of the end of June 2024)
EHS*1 Audit Based on PSCI*2
The Group implements EHS audits for overseas production sites every three years. There were no critical findings in the audits from FY2020 to FY2022. The summary of the results is as follows:
Implementation period: Mar. 2021 to Mar. 2024
Number of sites: 9 sites
Number of sites with findings (excluding minor findings): 8 sites
Number of findings: 37 cases
Responding to findings
Management System |
- Established Global BCP*3 Policy and BCP in each site
- Established relevant documents(regulations, SOPs, and guidelines, etc.) for each company based on the Global EHS Policy
|
Environment |
- Strengthened disposal management of liquid hazardous waste
- Installed acoustic barriers to mitigate noise from the equipment.
|
Health & Safety |
- Strengthened health and safety management through establishing/revising SOPs
- Mitigated exposure risks to body fluids for First Aid Responders through trainings, etc.
|
- *1EHS:Environment, Health and Safety.
- *2PSCI:Pharmaceutical Supply Chain Initiatives, non-profit organization which promotes sustainable procurement in the pharmaceutical and healthcare industry.
- *3BCP:Business Continuity Plan.
Environmental Auditing
Audits related to environmental management are conducted with three assessment approaches by the operating sites, the environmental management department (Sustainability Promotion Department) and ISO certifying bodies. These environmental audits supplement one another according to the situation at each operating site. Audits conducted by the Sustainability Promotion Department once every three years target all operating sites under the key theme of environment-related laws and regulations. In FY2023, audits were conducted at Daiichi Sankyo Co., Ltd.’s Head Office, Shinagawa Site, Kasai Site, Daiichi Sankyo Healthcare Co., Ltd.,, Daiichi Sankyo Pharmaceutical (Shanghai) Co., Ltd. Shanghai Plant, Daiichi Sankyo Brazil Farmaceutica Ltda Alphaville Plant. The audits confirmed that good compliance was being practiced in relation to environmental related laws and regulations and that there were no concerns with the potential of leading to major environmental risks.
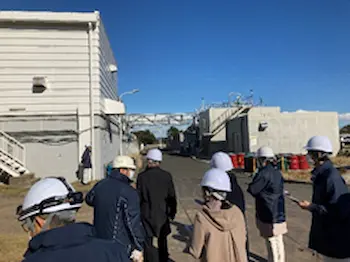
Conducting audits
Response to Accidents and Other Emergencies
Plants and research facilities with particularly high environmental risks have prepared protocols and defined responses to emergencies, including the prevention and mitigation of environmental pollution due to disasters and accidents. They also conduct periodic training and emergency drills while maintaining the necessary equipment.
In FY2023, no environmental accidents that have a significant impact on the surrounding environment occurred.
Environmental Education and Awareness Raising Activities
Workshops for environmental managers and initiatives to optimize environmental management
Every year, we hold a workshop for environmental managers on different themes that are relevant at the time to provide specialized education and information for those responsible for environmental-related tasks in domestic Group companies. In FY2023, we held alecture themed on key points of revision of the energy conservation law, in which approximately 50 people participated.
Workshops on global warming countermeasures
We hold workshops for global warming countermeasures every year to provide specialized education and share information on energy-saving and global warming countermeasures targeting facilities and energy managers of our plants and research facilities.In FY2023, a company gave a lecture on "High Efficiency High Temperature Heat Pumps for Industrial Applications" as an advanced technology in March 2024. Approximately 50 people participated in this workshop.We will continue to plan and hold workshops to promote energy conservation and global warming countermeasures.
Environmental e-learning
We provide environmental e-learning programs for all Group employees. In FY2023, the theme was on Current Status of Biodiversity and Its Impact on Our Lives. In domestic group companies, the participation rate was 97.4% among 9,926 applicable employees. For those who had not participated in the e-learning including new employees, we thoroughly informed them of and provided the voluntary e-learning program. The participation rate of the entire Group was approximately 98%.
Environmental Art Contest
We implement environmental communication measures to improve employees’ environmental awareness. Every year in June, which is designated as “Environment Month” by the Group, a contest is held for artwork that gives the viewer an impression of the environment. We accept entries from Group employees and their families globally
For the FY2023 contest, we received a total of 1,796 entries from Group companies in Japan and overseas. Specifically, we received 529 entries from domestic Group companies and 130 entries from overseas Group companies in the image category; 1,059 entries in the senryu (humorous or ironic haiku) category targeting domestic Group companies; and 78 entries in the slogan category targeting overseas Group companies. We selected the top prize and SDG special prize winners, and held an online award ceremony.
Daiichi Sankyo Group COOL CHOICE Program*
We carried out the Daiichi Sankyo Group COOL CHOICE Program to raise environmental awareness in all employees and to encourage them to practice eco-friendly activities not only in their workplaces but also in their homes. The number of registered participants rose from 1,917 in FY2022 to 2,123 in FY2023. In support of the COOL CHOICE movement, which is a national movement for the prevention of global warming, the Group carries out the Daiichi Sankyo Group COOL CHOICE Program targeting employees of Group companies in Japan. This program allows employees to access a dedicated website and fill out information on the eco-friendly activities endorsed by the COOL CHOICE movement which they have been practicing at home and in the workplace. Points are granted according to the status of participation in the program and can be exchanged with eco-friendly goods or donated to environmental protection organizations. This program is held every summer from June to September, and since its start in FY2013, a total of approximately 13,400 employees have participated. From FY2024, the program is being implemented globally as One DS Climate Action.
*In support of the COOL CHOICE movement, which is a national movement for the prevention of global warming, the Group carries out the Daiichi Sankyo Group COOL CHOICE Program targeting employees of Group companies in Japan and their families.
Environmental Supply Chain Management
Sustainable Procurement
The Group has set out the Business Partner Code of Conduct (BPCC) in April 2019 in relation to the Daiichi Sankyo Group Procurement Policy, in line with the revision of the Daiichi Sankyo Group Corporate Conduct Charter.
This BPCC sets out expectations for the promotion of sustainable procurement to business partners that provide products and services to us. In the BPCC, the environment-related items are as follows(see 4. Promoting Environmental Management).
Business Partner Code of Conduct
4. Promoting Environmental Management
(1) Reduce greenhouse gas emissions
(2) Appropriately manage waste and emissions
(3) Prevent and mitigate spills and releases
(4) Promote energy and resource conservation
(5) Support biodiversity
The Daiichi Sankyo Group requests its major business partners to conduct a Sustainable Survey every three years based on the Business Partner Code of Conduct, in order to deepen their understanding of our Group’s thinking and strengthen communication with them.
For more details.
Attained Leaderboard 5 Years in a Row, the CDP’s Highest Supplier Engagement Rating
Recognized by the international environmental NGO CDP* for taking climate change measures in the supply chain and carrying out activities to reduce greenhouse gas emissions, for five years in a row we have been listed on the CDP’s Supplier Engagement Leaderboard for taking the highest rating in its Supplier Engagement Rating. The CDP runs a program in which it evaluates suppliers’ climate change initiatives in accordance with requests from companies. In FY2023, the CDP placed 458 companies on the Supplier Engagement Leaderboard, which are the top 2% of companies evaluated. Among them 109 were Japanese companies, including Daiichi Sankyo. We were also placed on the CDP’s climate change A List 2023, its highest rating for climate change for four years in a row.
.webp?385)
*NPO whose main activities consist of asking companies and local governments to disclose information on initiatives to address environmental problems such as climate change measures, water security, and forest conservation in accordance with requests from institutional investors and major purchasing organizations worldwide that have a high interest in environmental issues, and thereby incentivizing environmental action.
Environmental Supply Chain Management
Choice of raw material or components that have a lower environmental footprint
- To reduce the environmental impact of our synthetic APIs, we evaluate the environmental impact of manufacturing processes for each product at each development stage. At the beginning of product development, the assessment values of manufacturing processes are calculated to identify items with high values in toxicity and hazardousness, energy consumption, and emissions.
- Manufacturing processes are continuously improved and evaluated by re-calculating the values at each development stage through the EHS management program.
- In order to reduce the environmental impact in material procurement and manufacturing process development, we have started using the process analysis tool to quantify the CO2 emissions in manufacturing process for biopharmaceuticals.
- We are promoting a switch from petroleum-derived plastics to biomass plastics for packaging materials to reduce the environmental burden. We have already switched to biomass materials of plastic bottles for solid oral dosage and syringe trays.
Direct operation, production & manufacturing
- The Daiichi Sankyo Group promotes the optimization of the EMS in accordance with the Standard for the Daiichi Sankyo Group’s Environmental Management Systems. Production sites that use large amounts of energy for manufacturing in Daiichi Sankyo Group have acquired the international standard for the EMS, ISO14001 certification. Our ISO 14001 certification rate is now 89.2% (based on CO2 emissions).
- At all sites, including these production sites, we set annual environmental targets for energy, water, and waste and work to reduce them.
- For waste-related cases, we are working to reduce waste from expired inventory by commonizing raw materials through platforming of the manufacturing process for the development of biopharmaceuticals.
- In addition, when concluding a quality contract, we request suppliers to submit SDS (Safety Data Sheets) to confirm information on chemical substances contained in raw materials (properties, hazards, toxicity, and handling, etc.).
Distribution, storage and transportation
- Regarding commercial distribution, we are promoting the following initiatives: (1) use of solar power generation systems at warehouses, (2) reduction of CO2 emissions during transportation through joint delivery, and (3) switch to recyclable pallets.
- For safe handling of products, we share SDS (Safety Data Sheets) with drivers and business partners who transport our products.
Use phase – operation and servicing/maintenance
- We are reducing obsolescence rates of drugs in clinical trials by sharing clinical trial materials across multiple protocols.
- In addition, we have reduced the amount of expired control drugs by optimizing the procurement of control drugs in clinical trials (procurement of smaller quantities, more frequently, and drugs with longer expiration dates).
End of life management
- Daiichi Sankyo Healthcare has started Japan's first demonstration experiment of the “After use PTP Sheet Recycling Program” in the city of Yokoham in October 2022.
- As of the end of September 2024, the collection sites were set up at 102 locations in pharmacies, drugstores, hospitals, and public facilities and a cumulative total of approximately 5 tons of used PTP sheets have been collected. The collected PTPs are recycled into new products. Collection boxes are also available at the Daiichi Sankyo Kusuri Museum on the first floor of its Tokyo headquarters,